Business Advice4 min
Basement Sub-Flooring Options
Making a basement a usable living space that people can enjoy starts with the right sub-flooring option. Concrete is hard and uncomfortable. It’s porous and can be cold in the winter and musty in the summer. With the right premium grade sub-flooring installed correctly, you can achieve a comfortable floor that delivers warmth and enjoyment.
What Is The Best Sub-Flooring Option?
Choosing a premium sub-flooring is always a good option, but it is almost a must when deciding what sub-flooring option is best for a basement. With moisture being an issue in basement spaces, LP Legacy® Premium Sub-Flooring offers the protection you need. Proven to be one of the stiffest sub-floors on the planet, LP Legacy panels are packed with more strands, resin and wax to provide exceptional resistance to moisture and edge swell. The resin uses a Gorilla Glue Technology®, which also contributes to outstanding stiffness.
Often, codes require a greater-than-normal load-bearing capacity of the sub-floor or floor system for basements. As one of the strongest sub-floorings on the market, LP Legacy sub-flooring easily meets any code requirement when it comes to strength. Additionally, the panels are manufactured with remarkable consistency, making it easier to level the floor.
Best Practice For Installation
You may wonder if you can put sub-flooring over concrete. While the application of placing a single layer of LP Legacy sub-flooring directly over concrete is prohibited, there is a preferred method that is code approved. Below is a quick overview of this method.
Install a water vapor barrier directly over the concrete, if using untreated supports, which would need to be mechanically fastened to the concrete. If using treated supports, the vapor barrier can be placed over the supports, which also allows the builder to fasten the supports with a construction adhesive.
Install wood support members, spaced as desired. This is also an opportunity to level the surface in the likely event the concrete has an undesired slope.
Place insulation between the wood structural supports (e.g. 1˝ foam, which typically provides an R-factor of 5).
Apply the LP Legacy sub-flooring using the normal, approved installation method.
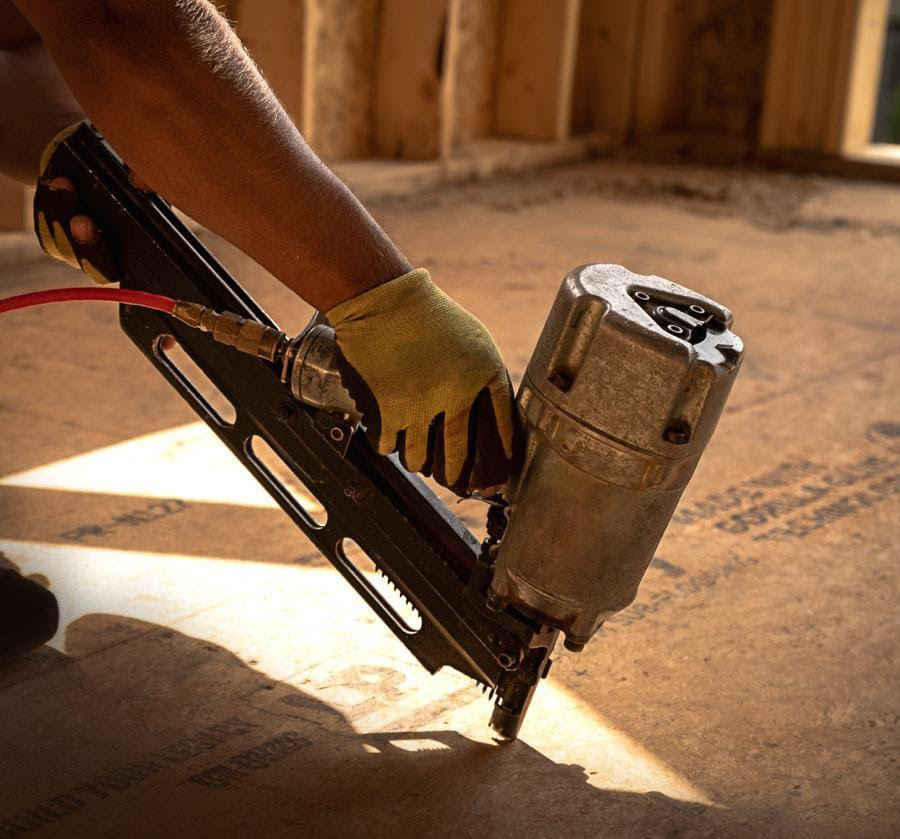
As mentioned before, insulation is recommended between supports. How much is based on local building code requirements and can change depending on where you live. It’s always good practice to check with local building authorities. Unless the sub-flooring is going to be exposed to the elements for an extended period of time, we do not recommend waterproofing the basement sub-floors. In such cases, the builder would avoid polyurethane-based products.
If you are looking to create a livable basement that provides year-round comfort, start by installing LP Legacy sub-flooring. It will provide the foundation of a basement that homeowners can enjoy for years to come.
Want to know more about building with LP Legacy Premium Sub-Flooring? Discover all of its benefits here.
Continue Reading
Resiliency Solutions
5 minIntroducing LP® SmartSide® ExpertFinish® Naturals Collection™: Nature-Inspired Beauty Meets Engineered Performance
We’re excited to introduce the LP® SmartSide® ExpertFinish® Naturals Collection™, a bold new addition to our trusted line of engineered wood siding and trim that delivers the warmth and beauty of nature with the advanced protection and performance builders and homeowners expect.
Labor Solutions
5 minChoosing the Right LP® Structural Solutions Product for Your Build
When it comes to building strong, reliable, and high-performing structures, the materials you choose matter. At LP Building Solutions, we understand that every project, whether it’s a single-family home or a multifamily development, requires structural components that meet your needs for strength, durability, and efficiency.
Sustainability Solutions
5 minBuilding a More Sustainable Future with LP Building Solutions
In today’s world, sustainability is no longer just a buzzword, it’s a blueprint for responsible living and smarter building. As the construction industry seeks ways to reduce its environmental footprint, LP Building Solutions is focused on providing innovative building materials for eco-conscious builders to help reshape what it means to build sustainably
News & Stories3 min
History of Partnership with Gary Sinise Foundation
The LP Foundation is a proud partner of the Gary Sinise Foundation, which supports wounded veterans in several ways. You can learn more about the LP Foundation here.