Industry Trends3 min
How Resiliency Factors into Building Code Requirements
Historically, updates to building codes are adopted slowly across the United States. From state to state, builders often follow different codes depending on how recently code updates in their area have been implemented. This means it’s up to individual builders to determine how closely they’ll follow the industry’s best practices.
Building with resilient materials is among the industry’s top concerns, and it’s beginning to factor into building code requirements and development. This shows that taking measures for increased resiliency may soon be a requirement, not only a best practice. Let’s take a look at this trend, how codes and resiliency connect, and how the LP® Structural Solutions portfolio can help builders meet code while contributing to a more resilient build.
What Is Resiliency and Why Does It Matter?
The AIA’s Industry Statement on Resilience defines resiliency as “the ability to prepare and plan for, absorb, recover from, and more successfully adapt to adverse events." According to the National Oceanic and Atmospheric Administration (NOAA), billion-dollar weather disasters have increased over time, with 338 in total since 1980 and 56 in the past three years alone.
Beyond typical weather, moisture and energy concerns, resiliency is a critical issue in light of high-risk natural disasters—both in terms of the financial resources it takes to rebuild and the growing threat to the people who live in certain areas of the country.
When the industry prioritizes building with resilient materials, the impact reaches beyond a single home—we’re contributing to our purpose of Building a Better World™, helping to create a safe, secure place for people to call home.
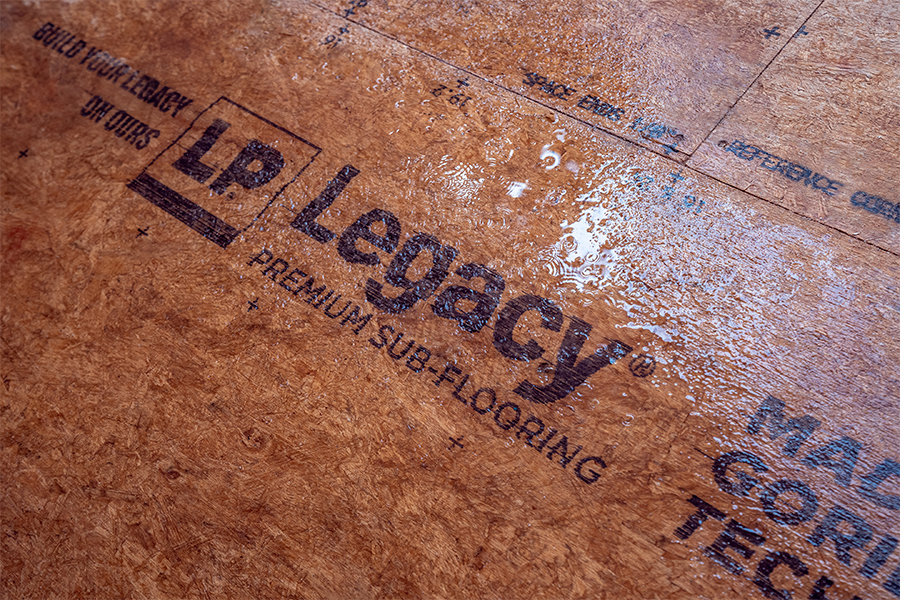
How Can Building Code Requirements Contribute to More Resilient Structures?
First of all, why are building codes important?
In a whitepaper by the International Code Council®, the organization notes that “building codes are an essential strategy in achieving resilience. [They] provide minimum requirements to protect life-safety in the built environment—every day and particularly in the face of hazards.”
“Resiliency becomes more about building scientists identifying problems and offering solutions,” says Neil Freidberg, Building Science Manager at LP Building Solutions.
Importantly, resiliency can be achieved when codes are coordinated across different threats, such as moisture, fire, durability, energy efficiency and more. “A product can be resilient in itself, but we want to talk about the building as a whole being resilient—not just a single component,” says Freidberg. “It’s a systems approach, and LP has products for all systems.”
Despite code updates that lean into building with resilient materials, code adoption varies among states. “Typically, it takes 5–6 years from when a new building code requirement is published to full adoption,” Freidberg says. “Some will still allow variances from the latest code so they fall back to previous codes.”
Though they can always build beyond building code requirements, builders may choose to stick to what they know and what makes the most financial sense before fully adopting a new requirement—thus creating a wide range of resiliency throughout the country.
Building With Resilient Materials That Meet Code
LP Structural Solutions products can help builders meet code requirements, no matter where a build is located, and still boost their structure’s resiliency. For example, LP® FlameBlock® Fire-Rated Sheathing helps builders meet code for fire-resistant construction while adding structural strength and retaining design flexibility. LP WeatherLogic® Air & Water Barrier can serve as part of a wall assembly designed for strength and for moisture resistance.
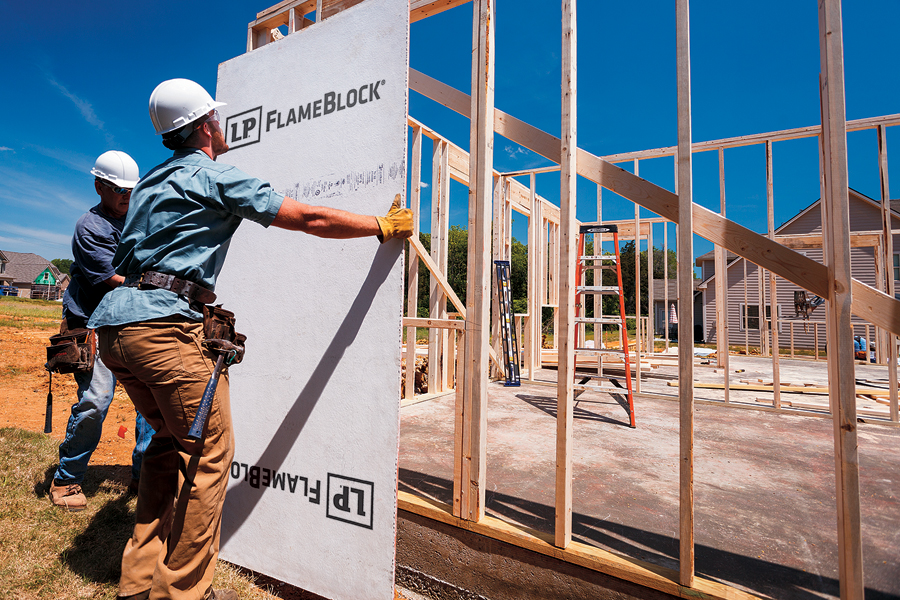
The Bigger Picture: A More Sustainable World
At LP, everything we do ladders up to our core purpose: Building a Better World™. Ultimately, resiliency isn’t just about avoiding costly rebuilds—it’s about sustaining the people around us and communities in which they live.
Resilience plays a key role in vulnerable communities where extended impacts of severe weather can take a significant toll. That’s why structural resiliency is just one piece of the puzzle—but it’s one we take seriously.
Building to address specific types of weather and location can help you decide what products to use. As building code requirements skew stricter with an intent to bolster resiliency, building professionals can help lead the way with quick adoption and shifting to premium products designed to help them build better.
Continue Reading
Resiliency Solutions
5 minIntroducing LP® SmartSide® ExpertFinish® Naturals Collection™: Nature-Inspired Beauty Meets Engineered Performance
We’re excited to introduce the LP® SmartSide® ExpertFinish® Naturals Collection™, a bold new addition to our trusted line of engineered wood siding and trim that delivers the warmth and beauty of nature with the advanced protection and performance builders and homeowners expect.
Labor Solutions
5 minChoosing the Right LP® Structural Solutions Product for Your Build
When it comes to building strong, reliable, and high-performing structures, the materials you choose matter. At LP Building Solutions, we understand that every project, whether it’s a single-family home or a multifamily development, requires structural components that meet your needs for strength, durability, and efficiency.
Sustainability Solutions
5 minBuilding a More Sustainable Future with LP Building Solutions
In today’s world, sustainability is no longer just a buzzword, it’s a blueprint for responsible living and smarter building. As the construction industry seeks ways to reduce its environmental footprint, LP Building Solutions is focused on providing innovative building materials for eco-conscious builders to help reshape what it means to build sustainably
News & Stories3 min
History of Partnership with Gary Sinise Foundation
The LP Foundation is a proud partner of the Gary Sinise Foundation, which supports wounded veterans in several ways. You can learn more about the LP Foundation here.