Industry Trends4 min
LP TopNotch 350 Durable Sub-Flooring vs. The Elements
Delayed timelines are a headache. However, when you’re subject to the elements, supply chain issues and client schedules, timeline adjustments are often unavoidable. Though you don’t have influence over many of these factors, you can choose the materials you build with—and choosing sub-flooring like LP® TopNotch® 350 Durable Sub-Flooring will be your best bet for getting back on track.
Can OSB Be Used for a Sub-Floor?
Yes, premium OSB sub-flooring is not only allowable but a great solution for structures that are exposed to the elements during construction.
OSB sub-flooring like LP TopNotch 350 Durable Sub-Flooring is used by top builders looking for strength, stiffness and moisture resistance at a great price. Its surface is sanded for a uniform, smooth foundation for a variety of finished flooring. But the real benefit of LP TopNotch 350 panels for in-progress construction is the unique RainChannel® notch system.
Get Protection from the Elements with RainChannel® Technology
One of the biggest advantages of using premium OSB for sub-flooring is its ability to withstand moisture, especially rainfall, for which the RainChannel technology in LP TopNotch 350 panels is engineered.
LP TopNotch 350 sub-flooring is equipped with a self-draining notch system to drain water that accumulates on the surface of the panels. Combined with a moisture-resistant edge seal, the RainChannel system helps fight moisture absorption and edge swell, reducing the need for sanding.
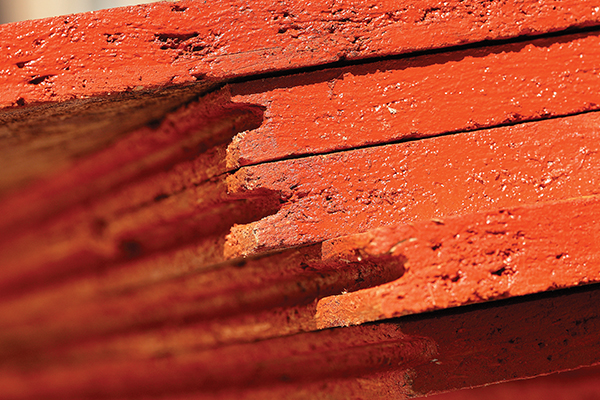
LP TopNotch 350 sub-flooring can also work in tandem with LP Legacy® Premium Sub-Flooring for moisture resistance in multi-level structures. Installing LP TopNotch 350 panels on lower floors allows quick evacuation for any water that accumulates during construction. Upper levels that may be exposed to more water from rainfall during construction can have additional safeguards in place, such as the Gorilla Glue Technology® built into LP Legacy panels for premium moisture resistance.
You Made it Through Construction—Now What?
Your sub-flooring is part of the foundation of your home, and there’s no doubt LP TopNotch 350 Durable Sub-Flooring sets you up for success long after construction—after all, your clients will be living on top of this sub-flooring for years to come.
LP TopNotch 350 sub-flooring is engineered for incredible strength and stiffness, offering a more stable floor for your clients. Take the quality of your installation to the next level by pairing LP TopNotch panels with LP Legacy Sub-Floor Adhesive. When used together, these products have a squeak-free lifetime limited warranty.
For more information on LP TopNotch 350 Sub-Flooring, find product specifications, installation instructions, complete warranty details and more here.
Continue Reading
Resiliency Solutions
5 minIntroducing LP® SmartSide® ExpertFinish® Naturals Collection™: Nature-Inspired Beauty Meets Engineered Performance
We’re excited to introduce the LP® SmartSide® ExpertFinish® Naturals Collection™, a bold new addition to our trusted line of engineered wood siding and trim that delivers the warmth and beauty of nature with the advanced protection and performance builders and homeowners expect.
Labor Solutions
5 minChoosing the Right LP® Structural Solutions Product for Your Build
When it comes to building strong, reliable, and high-performing structures, the materials you choose matter. At LP Building Solutions, we understand that every project, whether it’s a single-family home or a multifamily development, requires structural components that meet your needs for strength, durability, and efficiency.
Sustainability Solutions
5 minBuilding a More Sustainable Future with LP Building Solutions
In today’s world, sustainability is no longer just a buzzword, it’s a blueprint for responsible living and smarter building. As the construction industry seeks ways to reduce its environmental footprint, LP Building Solutions is focused on providing innovative building materials for eco-conscious builders to help reshape what it means to build sustainably
News & Stories3 min
History of Partnership with Gary Sinise Foundation
The LP Foundation is a proud partner of the Gary Sinise Foundation, which supports wounded veterans in several ways. You can learn more about the LP Foundation here.