Business Advice5 min
Radiant Barrier vs. Insulation : How to Choose Between Radiant Barrier Sheathing and Spray Foam Insulation
In recent years, homebuyers have shifted toward more energy-efficient homes, a trend you’ve likely discovered in the selections your clients are making including construction materials, finishes and appliances. Research has shown the cooler the attic space, the less time the home’s air conditioning unit must run to keep the living space comfortable.
If you’re a builder weighing the choice between radiant barrier sheathing versus spray foam insulation to reduce attic heat, there are many factors to consider. And it’s likely your customers have questions about the difference between attic spray foam and radiant barrier as well.
What is the difference between radiant barrier and insulation?
Radiant barriers consist of a reflective surface bonded to a sheathing material, such as engineered wood. Typically installed in attics, radiant barriers reduce radiant heat transfer and tend to be more effective in warmer climates.
Installed throughout a home, insulation regulates the flow of heat. Essentially, it protects in the winter by retaining heat in the home and in the summer by keeping the heat out. It can be made of many different materials, such as spray foam, rigid foam or loose fill.
Do you need insulation with a radiant barrier?
Spray foam insulation should never be installed in direct contact with radiant barriers. This will negate the function of the radiant barrier because an air gap is required for the radiant barrier to work properly in reducing radiant heat. Radiant barrier sheathing can provide impressive temperature reductions in attics while also offering structural strength.
Can you use a radiant barrier instead of insulation?
No, radiant barriers cannot replace insulation. The code does not recognize any R-value from a radiant barrier. Spray foam has become increasingly popular because of the ease of installation. However, radiant barriers, such as LP® TechShield® Radiant Barrier, help keep heat from emitting into the attic space in the first place, cooling attic temperatures by up to 30°F.
Can insulating spray foam still be used with radiant barriers?
Radiant barriers must be installed with an air gap. LP recommends a minimum of 3/4” air space between the barrier and the foam.
There are other aspects of the radiant barrier vs. insulation story:
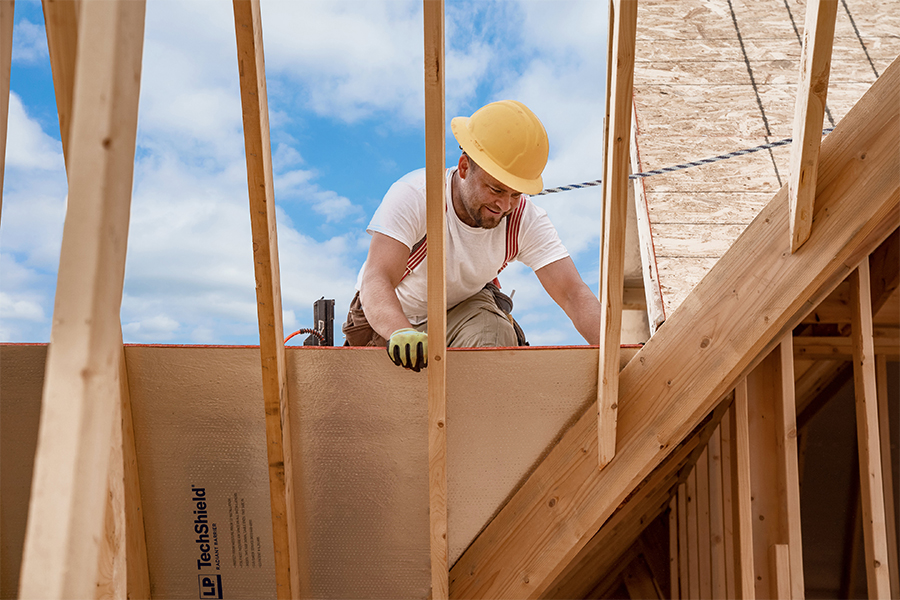
Proven Durability: Traditional vented attic assemblies with radiant barriers have a long history of reliable performance. Such systems allow for continuous drying of roofing materials during construction and throughout the life of the structure. Spray foam applied to the underside of the roof deck has the potential to trap moisture caused by roof leaks, potentially leading to rot and decay of the roof framing. These issues may go unnoticed for years until it’s too late.
Complementary Systems: Attic insulation works by slowing conductive heat flow from the attic into the living space, whereas radiant barriers reduce radiant energy from heating the attic. This reduction in attic temperature significantly improves the efficiency of attic insulation. Combined, the two systems result in a highly energy-efficient and cost-effective solution.
Cost Efficiency: Spray foam is expensive, sometimes thousands of dollars more than other types of insulation. Additionally, spray foaming the entire roof deck consumes far more insulation than would be required on the attic floor in a typical vented attic assembly.
Better Ratio of Conditioned Space vs. Livable Space: When attic floor insulation is eliminated, foam-encapsulated attics significantly increase the volume of space the homeowner must pay to condition without increasing livable space.
Easier Installation: Radiant barrier sheathing doesn’t require any special expertise to install, while spray foam insulation requires highly trained installers using special equipment.
For more on LP® TechShield® Radiant Barrier sheathing, hear what Jordan Smith has to say about the product.
FAQs About Radiant Barriers
Does a radiant barrier attract lightning?
Structures with radiant barriers have not been proven to attract lightning at a higher rate than structures without them.
Does a radiant barrier affect Wi-Fi?
While metallic materials can impact signals, it is unlikely for a radiant barrier to be the cause of disrupted Wi-Fi.
How long does a radiant barrier last?
LP TechShield Radiant Barrier sheathing is designed to withstand the test of time as it’s manufactured for durability with wax and resin to create a strong OSB substrate. It’s also backed by a 20-year transferable limited warranty, showing LP’s confidence in the product’s functionality for years to come.
Looking for more information? Find everything you need to know about LP TechShield panels by clicking here.
Continue Reading
Resiliency Solutions
5 minIntroducing LP® SmartSide® ExpertFinish® Naturals Collection™: Nature-Inspired Beauty Meets Engineered Performance
We’re excited to introduce the LP® SmartSide® ExpertFinish® Naturals Collection™, a bold new addition to our trusted line of engineered wood siding and trim that delivers the warmth and beauty of nature with the advanced protection and performance builders and homeowners expect.
Labor Solutions
5 minChoosing the Right LP® Structural Solutions Product for Your Build
When it comes to building strong, reliable, and high-performing structures, the materials you choose matter. At LP Building Solutions, we understand that every project, whether it’s a single-family home or a multifamily development, requires structural components that meet your needs for strength, durability, and efficiency.
Sustainability Solutions
5 minBuilding a More Sustainable Future with LP Building Solutions
In today’s world, sustainability is no longer just a buzzword, it’s a blueprint for responsible living and smarter building. As the construction industry seeks ways to reduce its environmental footprint, LP Building Solutions is focused on providing innovative building materials for eco-conscious builders to help reshape what it means to build sustainably
News & Stories3 min
History of Partnership with Gary Sinise Foundation
The LP Foundation is a proud partner of the Gary Sinise Foundation, which supports wounded veterans in several ways. You can learn more about the LP Foundation here.