Practical Advice for Combatting High Humidity in Construction
Persistent rain is certainly frustrating on a jobsite, as excessive moisture causes delays and increases costs. Add heat and excessive humidity to the mix, and it seems moisture problems in construction are never-ending. Choosing high-performance materials is just one way to maximize your build’s moisture protection and combat high humidity in construction.
How Does Humidity Affect Building Construction?
We all know high humidity affects worker stamina, but humidity affects building materials as well. “Swings in the temperature greatly affect humidity,” explains Neil Freidberg, Building Science Manager at LP Building Solutions. “If you have a hot day and a cool front moves in during the evening, you will have moisture condensation on all your surfaces in the morning.”
Since humidity is measured by the amount of water vapor in the air, condensation results in bulk water. “The higher the humidity, the more time is needed for ‘drying in,’ which allows the moisture to naturally dry out,” says Freidberg. “If air isn’t circulated, all the moisture that condensed the evening before will re-condense and re-absorb into the building materials all over again.”
How LP WeatherLogic® Air & Water Barrier Helps Combat Humidity and Moisture
Moisture is a big threat to a tight, healthy building envelope. As fully integrated water-resistive panels, LP WeatherLogic Air & Water Barrier works to help keep water and moisture out caused by excessive humidity.
A critical part of the moisture management system is properly sealing the panels with LP WeatherLogic Seam & Flashing Tape to help keep water vapor out. For all-in-one moisture management, LP WeatherLogic Water Screen helps protect against moisture retention and the mold growth associated with high humidity.
When & Where Does It Make Sense to Use LP WeatherLogic Air & Water Barrier?
Water-resistive LP WeatherLogic panels, which can be used on both walls and roofs, also eliminate the need for housewrap.
“You want to use LP WeatherLogic panels wherever it rains and storms,” says Freidberg. “Think of it as a rain jacket for your build. Sometimes you can’t wrap a house properly before a storm hits. LP WeatherLogic Air & Water Barrier helps reduce time for installation with more time for drying in.”
How LP® TechShield® Radiant Barrier **Helps Combat Humidity and Moisture
**
As the sun heats the roof, radiant barrier panels help reduce the amount of heat released from the roof panels into the home’s attic. LP TechShield Radiant Barrier can help reduce attic temperatures and keep cooling costs down.
The patented VaporVents™ technology allows any trapped moisture to escape from the LP TechShield panels and dry more quickly during and after installation.
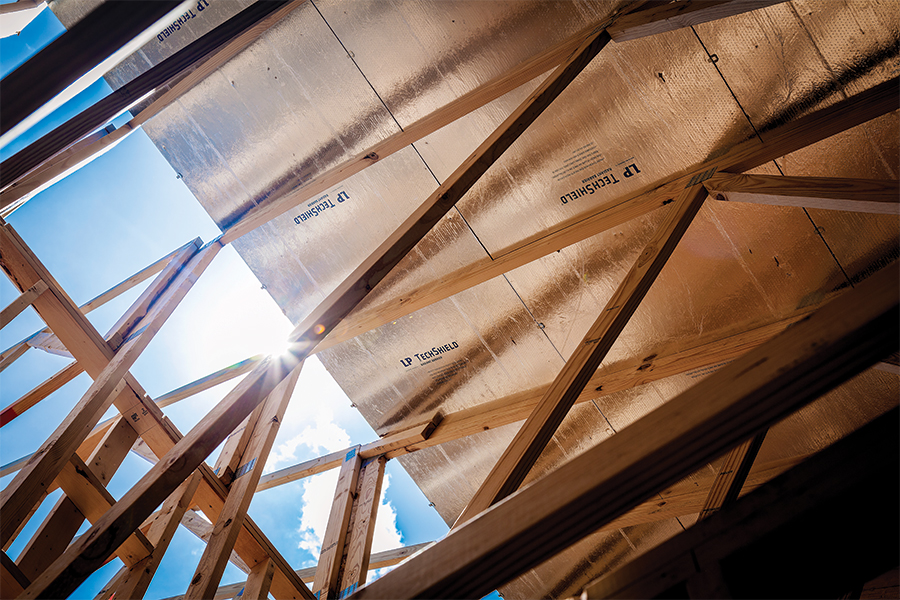
When & Where Does It Make Sense to Use LP TechShield Radiant Barrier?
Builders use radiant barriers to help reduce the impact of summer heat on home cooling costs. Building with LP TechShield Radiant Barrier has been proven to help block up to 97% of radiant heat transfer, helping to reduce attic temperatures by up to 30° F.
How LP Structural Solutions Products Help Combat Humidity and Moisture
Working in rainy conditions is a challenge, but adding high humidity to the mix makes it even more challenging. Evan Crowe is owner of CroweBuilt Homes in the greater Atlanta area, a southern region known for high humidity. Crowe turns to high-quality building materials to help get ahead of excessive moisture during new construction.
“One of my biggest problems is after rainfall, when the moisture lingers on all horizontal surfaces,” Crowe explains. “A high-quality sub-flooring product, such as LP Legacy® Premium Sub-Flooring with all its wax and resin, can withstand the rain and high humidity we experience in the Atlanta area.” LP Legacy sub-flooring is created with Gorilla Glue Technology® that provides excellent moisture resistance.
“If you don’t get things dried out, you can see mold or mildew. There’s an opportunity for studs to warp. They retain some of that moisture, and as you get further along with trades things dry, shrink and move around. Excessive moisture can cause things to no longer line up as they were and cause squeaks,” says Crowe. “LP Legacy panels help prevent squeaks.”
What Are Some Practical Tips for Building in Humid Climates?
“Use fans to expedite dry out,” says Freidberg. “Since heat rises and stores more moisture, I like to go from top to bottom. The hotter the air, the more moisture it carries. Start on the second story and blow hot air down to the first story as well as out toward open windows and doors.”
Freidberg says fans are a cheap and fast way to move air. As trades install concrete and mud drywall, too much moisture could extend drying time. Excessive humidity could wreak havoc on project timelines or cause moisture-related call-backs later from the homeowner.
Want to learn more about managing moisture problems? Read LP’s approach to moisture management.
Continue Reading
Resiliency Solutions
5 minIntroducing LP® SmartSide® ExpertFinish® Naturals Collection™: Nature-Inspired Beauty Meets Engineered Performance
We’re excited to introduce the LP® SmartSide® ExpertFinish® Naturals Collection™, a bold new addition to our trusted line of engineered wood siding and trim that delivers the warmth and beauty of nature with the advanced protection and performance builders and homeowners expect.
Labor Solutions
5 minChoosing the Right LP® Structural Solutions Product for Your Build
When it comes to building strong, reliable, and high-performing structures, the materials you choose matter. At LP Building Solutions, we understand that every project, whether it’s a single-family home or a multifamily development, requires structural components that meet your needs for strength, durability, and efficiency.
Sustainability Solutions
5 minBuilding a More Sustainable Future with LP Building Solutions
In today’s world, sustainability is no longer just a buzzword, it’s a blueprint for responsible living and smarter building. As the construction industry seeks ways to reduce its environmental footprint, LP Building Solutions is focused on providing innovative building materials for eco-conscious builders to help reshape what it means to build sustainably
News & Stories3 min
History of Partnership with Gary Sinise Foundation
The LP Foundation is a proud partner of the Gary Sinise Foundation, which supports wounded veterans in several ways. You can learn more about the LP Foundation here.