Business Advice4 min
Plywood Vs. OSB: Which is Better for Sub-floors?
When it’s time to construct sub-floors, you may automatically pick up either plywood or OSB without too much thought. During the COVID-19 pandemic you may have used whatever was most available, causing you to try different products. But have you ever stopped to think which one is better for sub-floors––OSB or plywood? Let’s compare OSB vs. plywood for sub-floors.
What is the difference between plywood and OSB?
Plywood is manufactured from thin layers of wood veneer glued together with the grain direction of each layer generally running at perpendicular angles to the adjacent layers. It’s made in a variety of thicknesses with general plywood categorized as 3-ply, 4-ply, 5-ply or multi-ply. APA uses 5-ply as a “catch-all” for five or more layers.
Oriented strand board (OSB) is also manufactured but, instead of layers of veneer, it’s made of layers of three- to four-inch strands oriented in opposing directions. OSB was initially introduced as a less expensive alternative to plywood, offering similar strength and stiffness.
Which is more water resistant—OSB or plywood?
Generally speaking, OSB absorbs moisture slower but plywood dries faster.
When plywood gets wet, it typically swells consistently across the sheet and then shrinks back to its normal dimension as it dries out. OSB tends to swell along the edges and will retain a portion of that misshapen edge after it dries out. However, since OSB takes longer to get saturated than plywood, it’s favored by some professionals.
Learn more about OSB and water resistance.
OSB vs. plywood: What is the best material to use for sub-floors?
Let’s take a look at the pros and cons of each so you can confidently choose between plywood and OSB.
Consistency: Because plywood consists of several large veneers of wood, you’re more likely to find knots, inconsistencies and soft spots. OSB is made by orienting and gluing together different strands, making it more structurally consistent. While OSB and plywood are about the same thickness, OSB is heavier and denser.
Water Absorption: When thinking about water absorption it’s easy to think about time spent on the jobsite, but if the homeowner experiences leaky plumbing or a flood a plywood subfloor could dry out faster, reducing the likelihood of trapped moisture turning moldy.
What’s the difference between commodity OSB and LP Legacy® Premium Sub-Flooring?
Commodity OSB and LP Legacy® Premium Sub-Flooring panels are made with the same general process. After logs are stranded, these strands are dried and then blended with waxes and resin. However, LP Legacy panels are more dense (with more wood fiber) and more resin is used, including resin made with Gorilla Glue Technology®, for superior strength and moisture resistance.
The real difference is when products like LP Legacy Premium Sub-Flooring panels are put to the test.
Professional builder Kyle Stumpenhorst performed a quick test to look at the differences in deflection between LP Legacy Premium Sub-Flooring, commodity OSB and plywood. Setting the panels up on supports measuring two feet apart, it was easy to see why LP Legacy sub-flooring is considered one of the stiffest sub-floor options on the market.
Stumpenhorst again put the sub-floor panels to the test and submerged LP Legacy sub-flooring and a commodity OSB product under water for three weeks. After this harsh test, the LP Legacy panel “still performed just as well as a brand new piece of LP Legacy sub-flooring,” Stumpenhorst concluded.
When comparing OSB and plywood sub-flooring, the LP Legacy sub-flooring warranty leads the industry and helps you stand behind your work. LP Legacy sub-flooring offers a Lifetime Limited Warranty, from the date of installation, and a Covered Until It’s Covered® No-Sand Warranty, from installation through the time finished flooring is installed over sub-flooring panels.
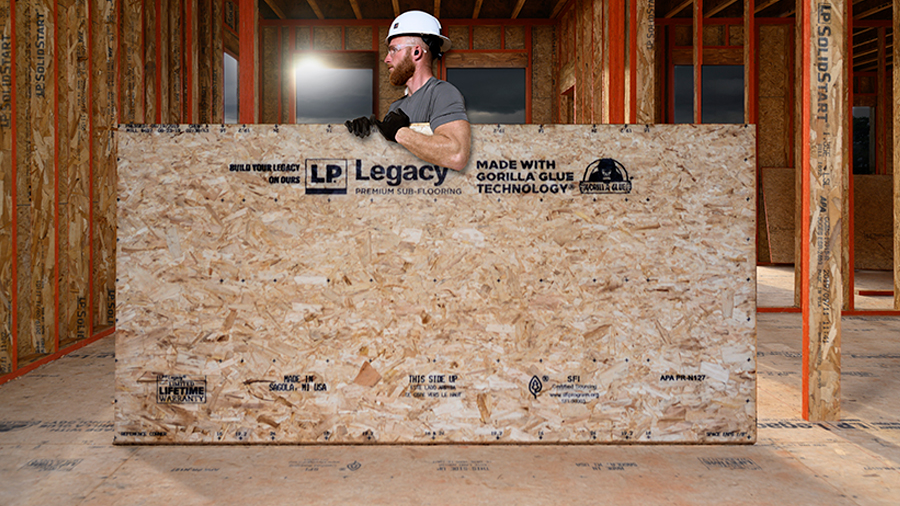
When should you use LP Legacy sub-flooring? Check out Mark LaLiberte, one of our partners at Construction Instruction, on his thoughts.
Continue Reading
Resiliency Solutions
5 minIntroducing LP® SmartSide® ExpertFinish® Naturals Collection™: Nature-Inspired Beauty Meets Engineered Performance
We’re excited to introduce the LP® SmartSide® ExpertFinish® Naturals Collection™, a bold new addition to our trusted line of engineered wood siding and trim that delivers the warmth and beauty of nature with the advanced protection and performance builders and homeowners expect.
Labor Solutions
5 minChoosing the Right LP® Structural Solutions Product for Your Build
When it comes to building strong, reliable, and high-performing structures, the materials you choose matter. At LP Building Solutions, we understand that every project, whether it’s a single-family home or a multifamily development, requires structural components that meet your needs for strength, durability, and efficiency.
Sustainability Solutions
5 minBuilding a More Sustainable Future with LP Building Solutions
In today’s world, sustainability is no longer just a buzzword, it’s a blueprint for responsible living and smarter building. As the construction industry seeks ways to reduce its environmental footprint, LP Building Solutions is focused on providing innovative building materials for eco-conscious builders to help reshape what it means to build sustainably
News & Stories3 min
History of Partnership with Gary Sinise Foundation
The LP Foundation is a proud partner of the Gary Sinise Foundation, which supports wounded veterans in several ways. You can learn more about the LP Foundation here.