News & Stories8 min
Specifying 1-Hour and 2-Hour Fire-Resistance-Rated Wall Assemblies
For about a century, architects and builders have used gypsum panels in wall assemblies to meet the criteria for 1- and 2-hour fire-resistance-rated wall assemblies. As product engineering develops, more and more architects are now looking for product solutions that bring added value to their 1-hour and 2-hour fire-resistance-rated wall assemblies.
Many are specifying LP® FlameBlock® Fire-Rated Sheathing because it meets code requirements for fire-resistant construction while potentially providing faster and easier installation than assemblies that use exterior gypsum and structural panels. They can also provide added design flexibility by reducing the overall wall thickness.
Why LP® FlameBlock® Sheathing for Fire-Resistance-Rated Assemblies?
With these design challenges in mind, LP Building Solutions created LP® FlameBlock® Fire-Rated Sheathing for low- and mid-rise wood and light gauge structures. LP FlameBlock sheathing may allow fire-resistance-rated walls to be constructed faster than common alternatives, potentially reducing labor costs while providing exceptional strength, durability and consistency.
UL fire-resistance-rated wall assemblies with LP FlameBlock sheathing provide several benefits to architects, engineers, builders, developers, contractors and even homeowners. LP FlameBlock sheathing wall assemblies provide design flexibility by combining structural capacity and fire resistance in a single panel. It may eliminate a layer of gypsum to help simplify and expedite the construction process. Potential cost savings may allow designers and builders to redirect the funds into design elements their clients are seeking, increasing the value of the property.
Let’s examine how LP FlameBlock sheathing can be used in a few different fire-resistance-rated wall assemblies.
Singe-Family Fire-Resistances-Rated Wall Assemblies
These UL assemblies are commonly used for single-family homes within close proximity of a property line.
UL Design No. V340: This assembly allows for 2x4 wall construction and is fire-resistance-rated for 1 hour from both sides.
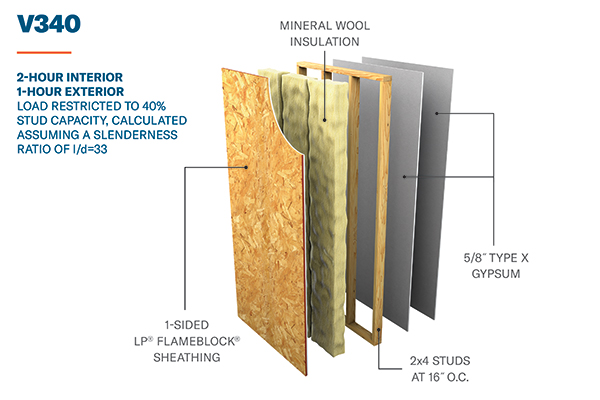
UL Design No. U348 (stucco): This assembly is used with stucco and is fire-resistance-rated for 1 hour from both sides.
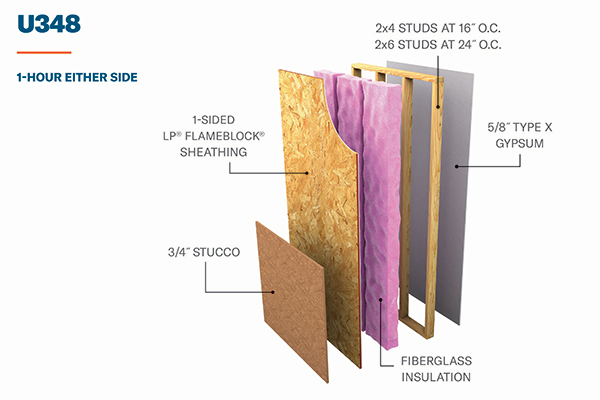
UL Design No. U348 (brick): This assembly is used with brick and is fire-resistance-rated for 1 hour from both sides.
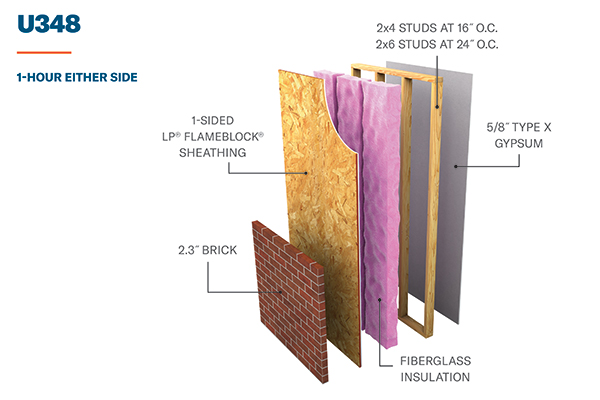
Benefits:
No exterior gypsum is required
Consistent wall thickness with unrated walls
Townhouse Fire-Resistance-Rated Wall Assemblies
These assemblies are typically used in dividing walls in townhouses.
UL Design No. V340 (Two 1-hour walls, back-to-back)
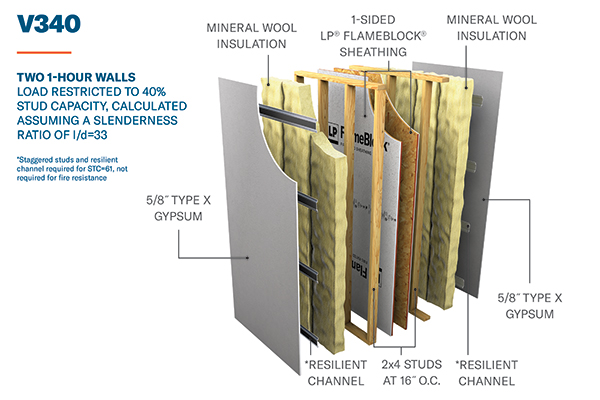
Benefit:
No code restrictions for mechanical, electrical and plumbing.
UL Design No. U350A and U350B (Common 2-hour fire-resistance-rated wall)
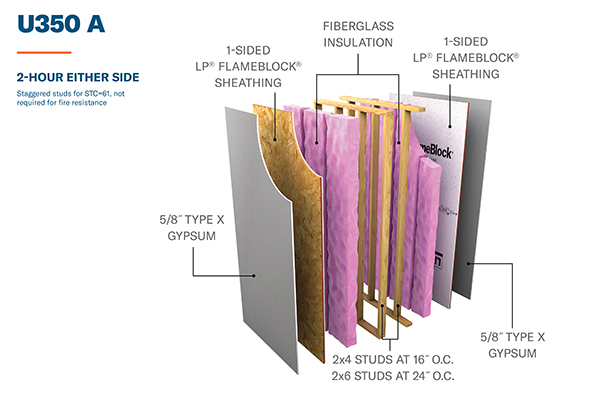
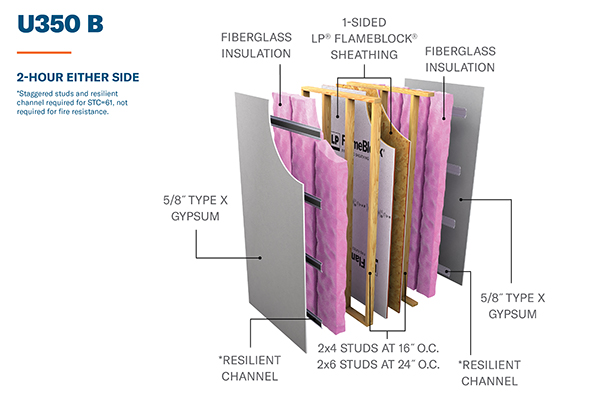
Benefits:
Alternative to a shaft wall system
Uses conventional framing practices
Sound Transmission Class (STC) rating of 61
Multifamily Fire-Resistance-Rated Wall Assemblies
UL Design U348: This is commonly used in Type V multifamily construction in load-bearing exterior walls. It also allows for the use of fiberglass insulation. This assembly is fire-resistance-rated for 1 hour from the interior side only, except when brick and stucco is the exterior facing.
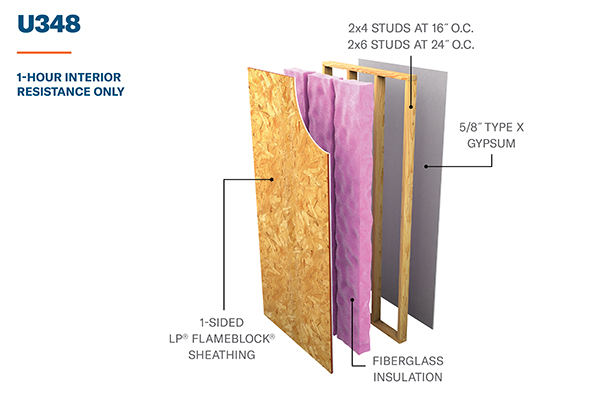
Mid-Rise Wall Assemblies
These assemblies are commonly used for Type III and Type V exterior walls.
UL Design No. V337 (1-hour from either side)
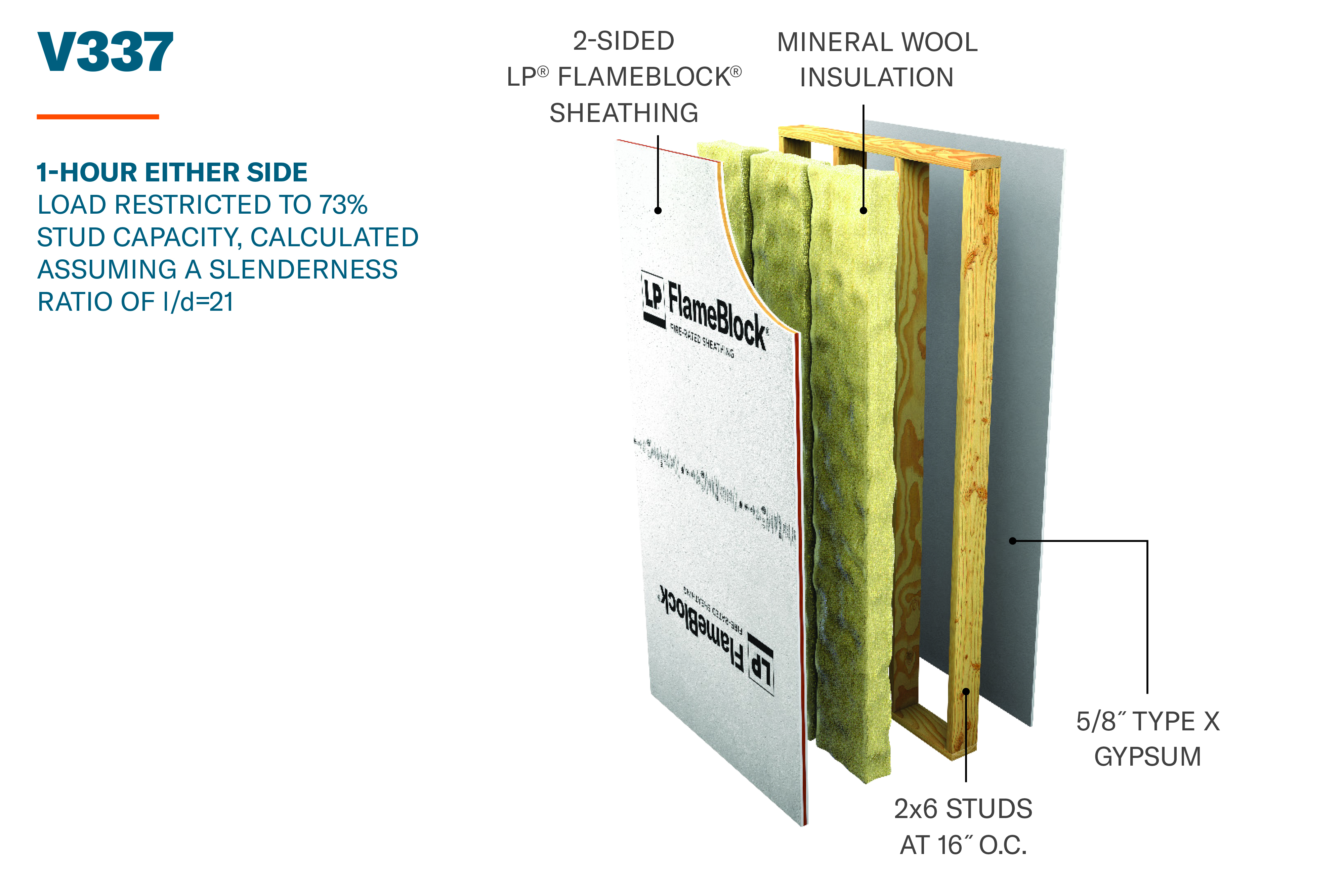
UL Design No. V337 (2-hour interior, 1-hour exterior)
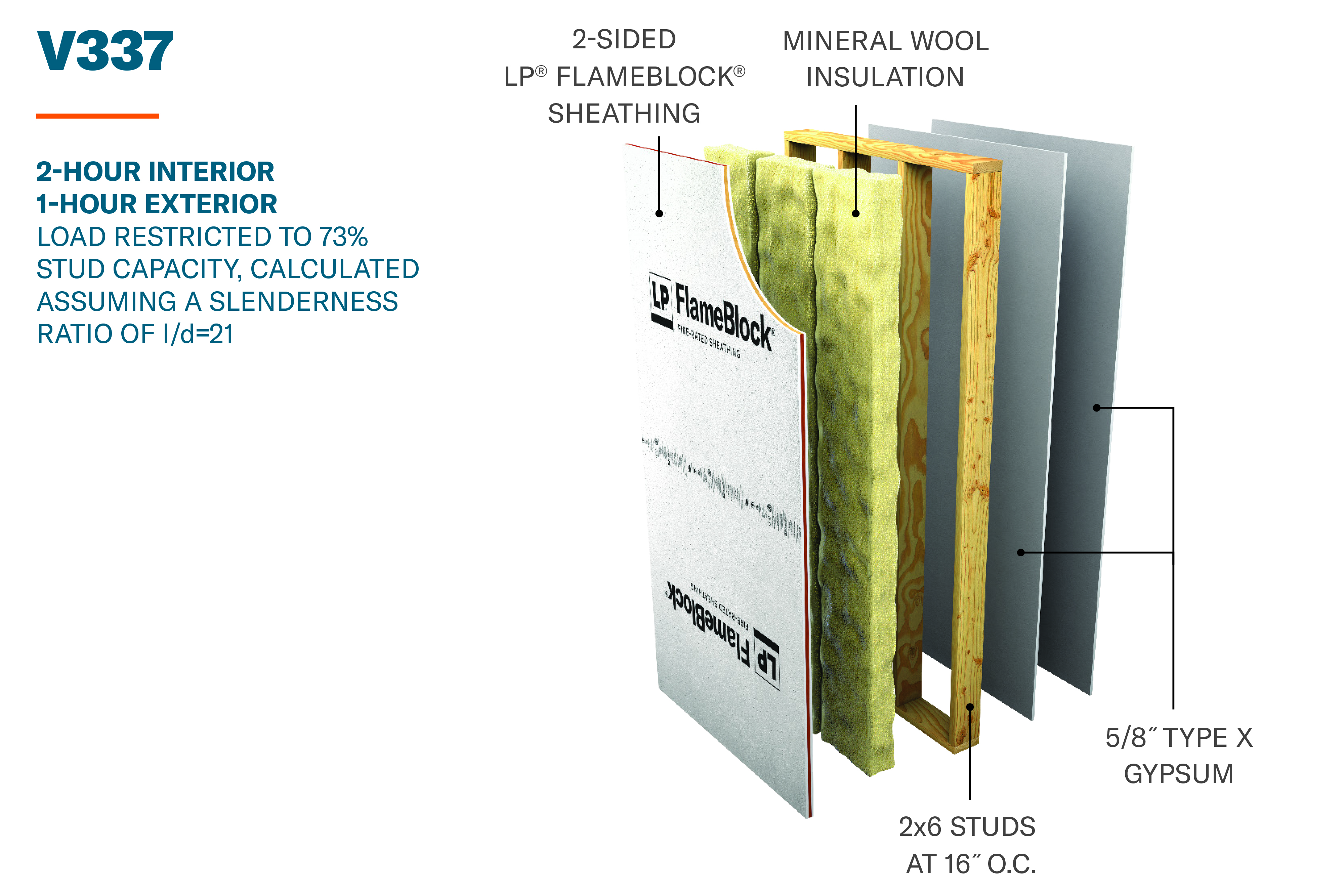
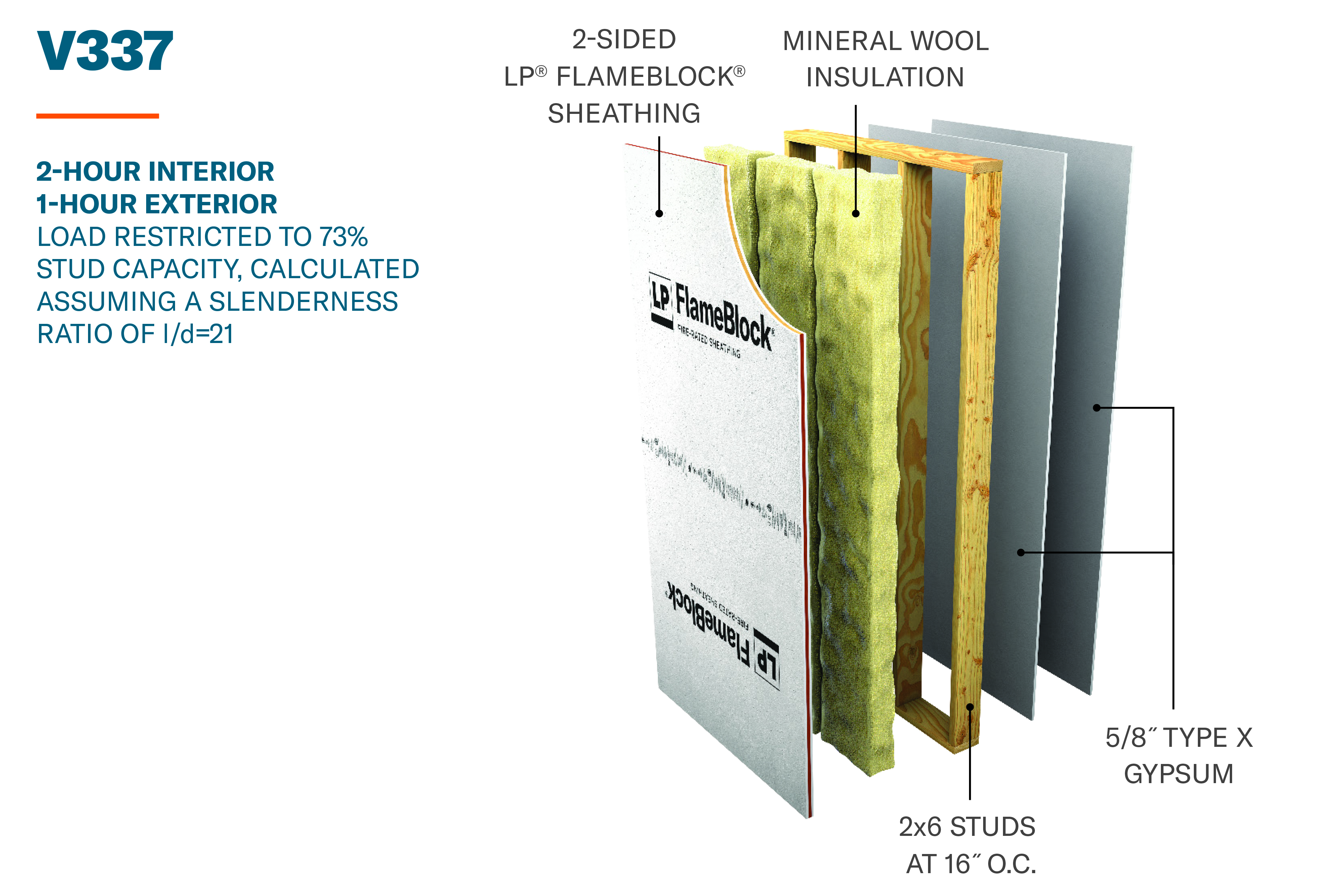
UL Design No. V340 (1-hour from either side)
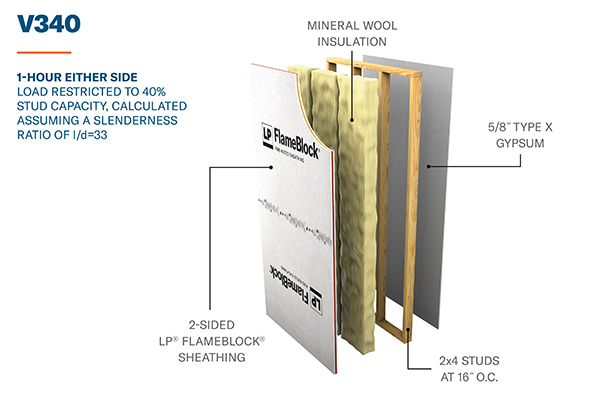
UL Design No. V340 (2-hour interior, 1-hour exterior)
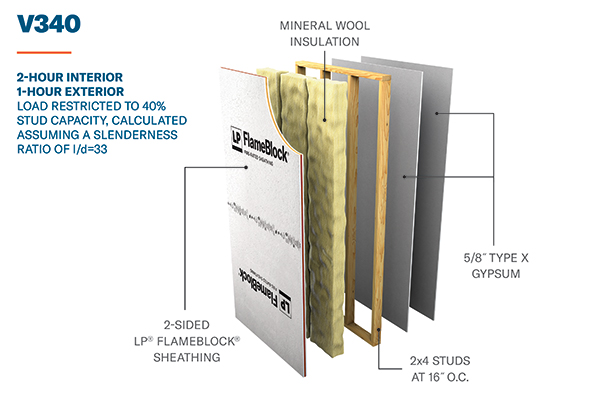
When using UL Design No. V340 assemblies for Type III exterior walls, 2-sided LP FlameBlock sheathing is required.
Benefit:
No exterior gypsum is required for exterior 1-hour fire-resistance rating
UL Design No. V337 with gypsum and V337 with stucco (2-hour from either side)
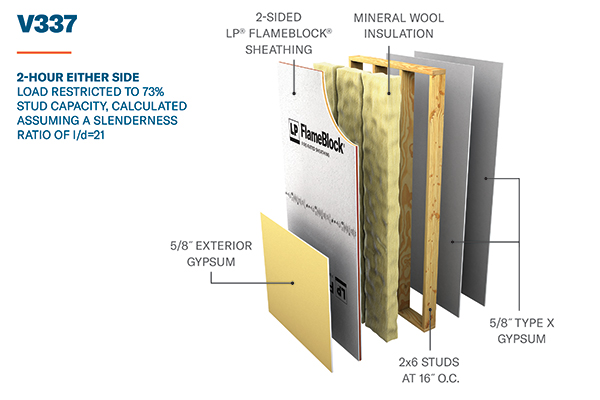
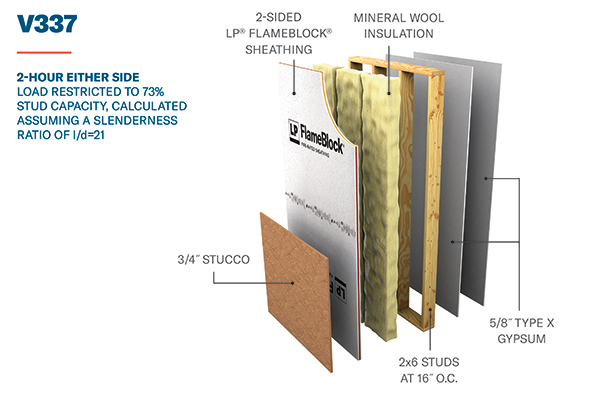
Benefits:
Potentially reduces the amount of exterior gypsum required
Base layer of interior gypsum may be replaced with 2-sided LP FlameBlock sheathing for double-sided shear walls
UL Design No. U349 (2-hour interior)
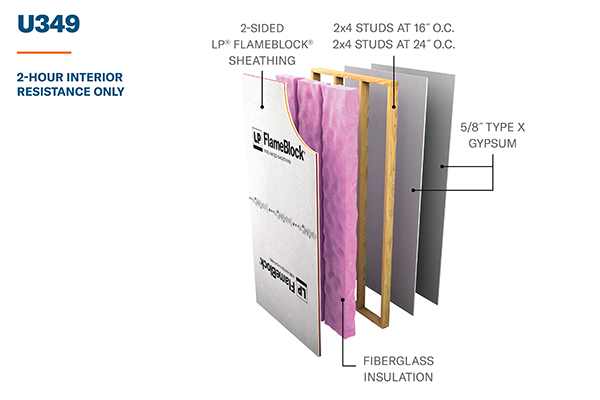
UL Design No. U349 (2-hour interior, 1-hour exterior)
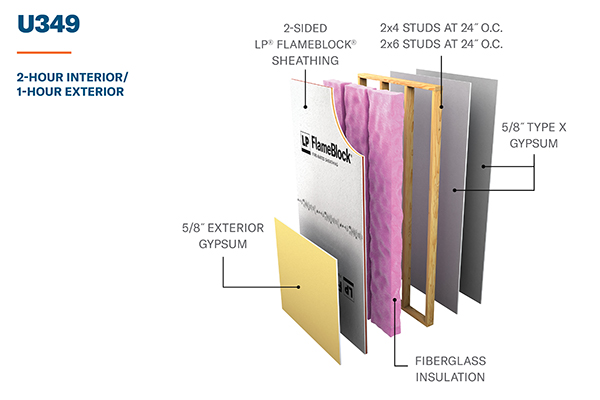
UL Design No. U349 (2-hour from either side)
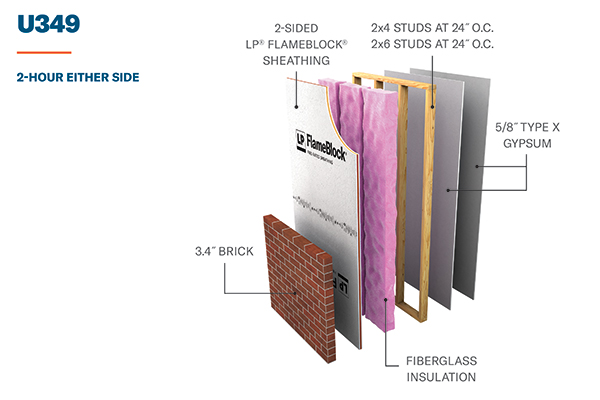
Benefits:
LP FlameBlock sheathing maintains the full strength of the substrate used
Some water-resistive coatings may be used in conjunction with LP FlameBlock sheathing
Code compliance does not have to limit design flexibility, budget or schedule. LP FlameBlock Fire-Rated Sheathing assemblies offer code-compliant solutions for a variety of building needs, including numerous UL assemblies for fire-resistance-rated wall systems. The OSB substrate of LP FlameBlock sheathing also has an Exposure 1 classification—which signifies that panels are intended to resist the effects of moisture on structural performance during active construction.
Fire-resistance-rated wall assemblies shouldn’t interfere with your design capabilities and construction schedules. Check out our LP FlameBlock page to learn more about the various assemblies.
Continue Reading
Resiliency Solutions
5 minIntroducing LP® SmartSide® ExpertFinish® Naturals Collection™: Nature-Inspired Beauty Meets Engineered Performance
We’re excited to introduce the LP® SmartSide® ExpertFinish® Naturals Collection™, a bold new addition to our trusted line of engineered wood siding and trim that delivers the warmth and beauty of nature with the advanced protection and performance builders and homeowners expect.
Labor Solutions
5 minChoosing the Right LP® Structural Solutions Product for Your Build
When it comes to building strong, reliable, and high-performing structures, the materials you choose matter. At LP Building Solutions, we understand that every project, whether it’s a single-family home or a multifamily development, requires structural components that meet your needs for strength, durability, and efficiency.
Sustainability Solutions
5 minBuilding a More Sustainable Future with LP Building Solutions
In today’s world, sustainability is no longer just a buzzword, it’s a blueprint for responsible living and smarter building. As the construction industry seeks ways to reduce its environmental footprint, LP Building Solutions is focused on providing innovative building materials for eco-conscious builders to help reshape what it means to build sustainably
News & Stories3 min
History of Partnership with Gary Sinise Foundation
The LP Foundation is a proud partner of the Gary Sinise Foundation, which supports wounded veterans in several ways. You can learn more about the LP Foundation here.