Industry Trends5 min
Sub-Floor for Heavy Tile Installation: Sub-Floor Materials for Tile
Many of the most popular floor trends in new home construction and remodeling are heavy porcelain, ceramic and stone floor tile. While these products promise long-term durability, it’s important you pay particular attention to the construction of the sub-floor to help minimize long-term damage. Let’s take a look at OSB subflooring for tiles and the best subfloor materials for tile.
Examples of Heavy Tile
You’ve likely seen an increase in large format and heavy floor tiles with your luxury and custom homebuyers, such as porcelain and ceramic tiles. While they are made from different densities of refined clay, in general porcelain and ceramic tiles are much heavier than more mainstream floor coverings. That’s why additional consideration needs to go into the design of floor systems that include ceramic, porcelain or stone tile.
How to Decide on Materials for Sub-Floor?
It’s critical to have homeowners choose design materials in the early planning stages of construction so you can prepare the structure accordingly.
For example, a commodity OSB sub-flooring is adequate if the homeowner chooses a budget-friendly vinyl, laminate or carpet. The weight of these common floor coverings is minimal compared to ceramic and porcelain tile or stone, which can be significantly heavier, especially considering that a backer board is also typically used.
By laying down natural stone or similar luxury tile and adding heavy furniture, you can quickly exceed the capacity of the sub-floor and the floor system. Without proper design, a floor system with commodity OSB sub-flooring for tile may experience excess deflection, cracking grout and tile and even separating the bond between the tile and the backer.
To minimize deflection, especially under heavy natural and porcelain stone, the best sub-floor for tile is a premium one. For example, LP Legacy® Premium Sub-Flooring is one of the toughest sub-flooring panels in the industry. The panels offer enhanced bending properties which, when adhered to properly designed floor joists with LP Legacy Premium Sub-Floor Adhesive, can result in less deflection of the overall floor system, protecting expensive floor coverings. And the greater strength of LP Legacy panels can help support heavy point loads like the legs of a piano.
Remember, always refer to floor design recommendations often provided by the industry association for the particular floor covering being used.
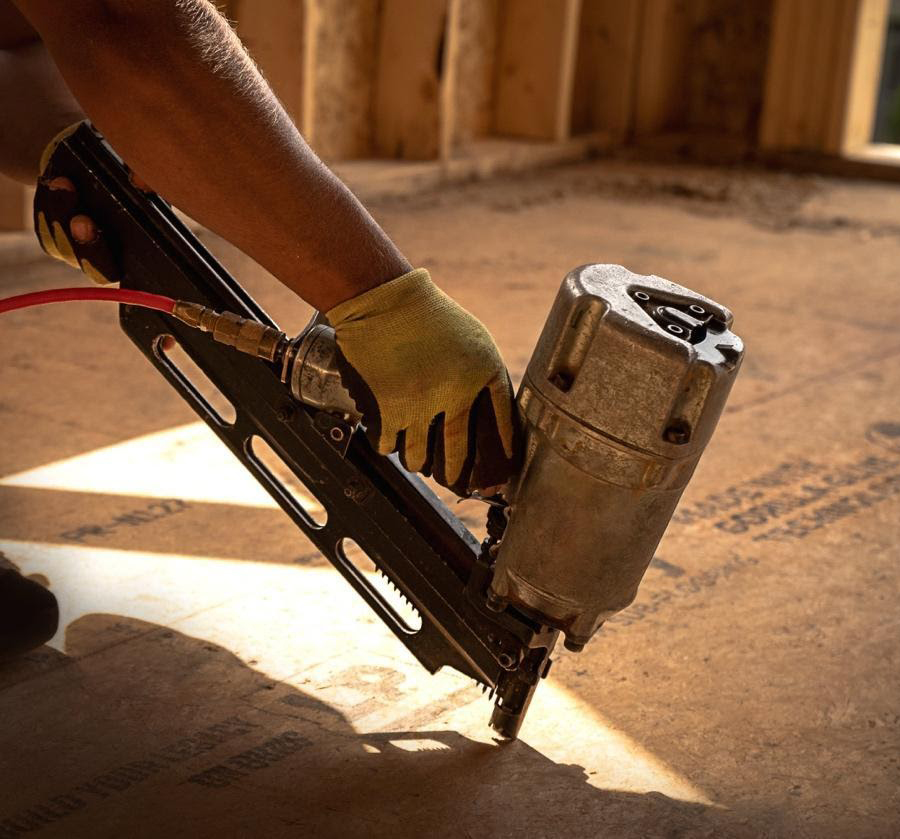
Subfloor Thickness and Materials for Tile
So how thick should the sub-floor be for tile? “It’s not necessarily about thickness, it’s about stiffness,” says Kelly Harmon, Senior OSB National Product Manager at LP Building Solutions. “For instance, a 23/32˝ LP Legacy Premium Sub-Flooring is 77% stiffer than a 19/32˝ panel of the same material placed in the same support system. Thickness greatly influences stiffness and subsequently deflection. Additionally, stiffness increases proportionally to the cube of the material’s thickness.”
LP Legacy Premium Sub-Flooring is a super-durable, premium panel designed for demanding sub-floor applications that require exceptional stiffness, providing the density and stability needed to support heavy stone and ceramic floors, exotic hardwoods and other heavy flooring options.
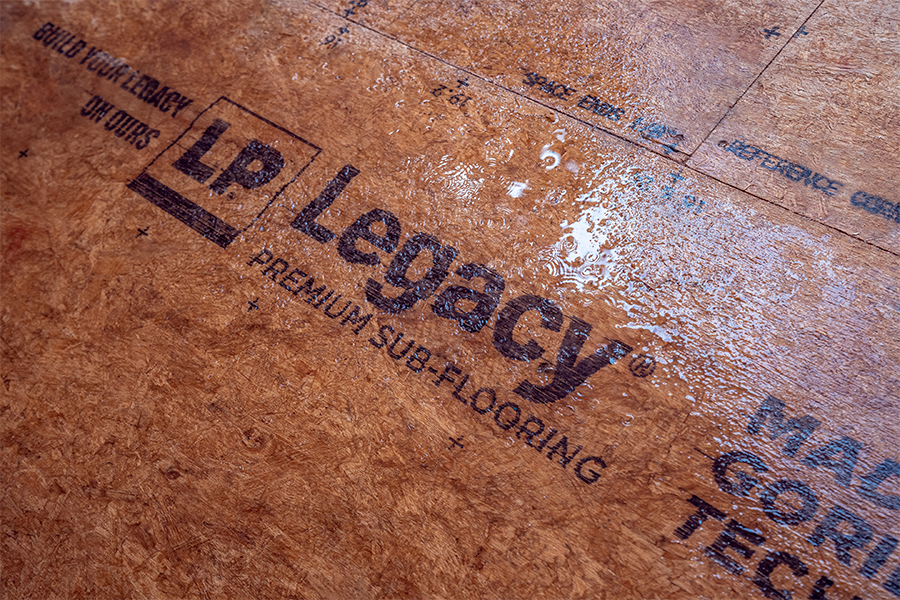
Preventing Uneven Sub-Flooring
An uneven floor can leave tile and stone partially unsupported which can quickly damage these expensive floor coverings. That’s why it’s important to choose a product designed to remain uniform, consistent and level. One of the benefits of using an option like LP Legacy Premium Sub-Flooring is its consistent, high-quality finishes. “LP Legacy sub-flooring has a full sand, which promotes uniform thickness. The transition between the panels in the profile and end joints is smooth. This helps avoid any elevation or step changes that could create a stress point under the tile,” says Harmon.
Is it worth switching to premium OSB products? Discover when it may be worth the upgrade.
Continue Reading
Resiliency Solutions
5 minIntroducing LP® SmartSide® ExpertFinish® Naturals Collection™: Nature-Inspired Beauty Meets Engineered Performance
We’re excited to introduce the LP® SmartSide® ExpertFinish® Naturals Collection™, a bold new addition to our trusted line of engineered wood siding and trim that delivers the warmth and beauty of nature with the advanced protection and performance builders and homeowners expect.
Labor Solutions
5 minChoosing the Right LP® Structural Solutions Product for Your Build
When it comes to building strong, reliable, and high-performing structures, the materials you choose matter. At LP Building Solutions, we understand that every project, whether it’s a single-family home or a multifamily development, requires structural components that meet your needs for strength, durability, and efficiency.
Sustainability Solutions
5 minBuilding a More Sustainable Future with LP Building Solutions
In today’s world, sustainability is no longer just a buzzword, it’s a blueprint for responsible living and smarter building. As the construction industry seeks ways to reduce its environmental footprint, LP Building Solutions is focused on providing innovative building materials for eco-conscious builders to help reshape what it means to build sustainably
News & Stories3 min
History of Partnership with Gary Sinise Foundation
The LP Foundation is a proud partner of the Gary Sinise Foundation, which supports wounded veterans in several ways. You can learn more about the LP Foundation here.