Industry Trends5 min
Tighter Building Envelopes
Overall, improvements in building envelopes have helped homeowners benefit from greater protection against moisture. Builders are able to create more energy-efficient homes overall due to these developments. However, when the exterior envelope doesn’t allow a structure to breathe, any moisture that gets trapped inside simply rots—causing more problems than intended.
What is the solution to needing a tight building envelope that allows for proper airflow? Symbiotic materials, such as the LP® Structural Solutions portfolio of products, provide an answer.
What Is a Building Envelope?
A building envelope is the separation of the interior and exterior of a building.
What is the function of a building envelope? These thresholds help facilitate airflow, protect a building from the elements, and assist with climate control and moisture protection. By definition, a building envelope’s job is to make the structure as energy efficient as possible, minimize leaks, and ensure ventilation is possible to prevent moisture buildup.
Building envelope science has developed considerably over the years as building technology has advanced. Many products contribute to the effectiveness of the building envelope, including sheathing, windows, doors, foundations, roofs and more. As each of these have advanced, the builder’s options for creating a tight building envelope have increased. However, building scientists have also found that symbiotic products—and companies that produce them with working together in mind—provide a better approach to building envelopes.
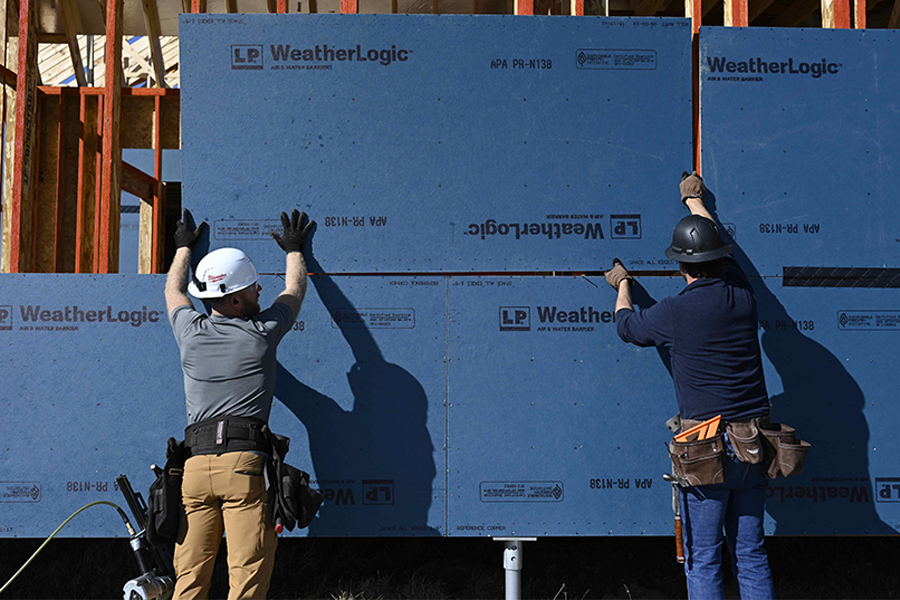
Building Envelope Maintenance
Building envelope maintenance is critical to ensuring the structure maintains its topnotch efficiency. A typical maintenance plan should cover all products that contribute to the exterior wall envelope, from roofing and windows to wall sheathing. Visual checks are the main way to ensure the building envelope is maintained; be sure to check all sealants and possible cracks and openings at least annually. It can also be useful to complete infrared surveys of these same components periodically so that even minuscule cracks can be discovered.
Types of Building Envelopes in Today’s Builds
Many different products can contribute to an exterior wall envelope. Here are a few examples of each component:
Roofing: Concrete, commonly used in commercial building envelopes, offers strength and fire-resistant qualities. Other roofing options include plywood and OSB products, often paired with asphalt shingles.
Wall Sheathing: Sheathing made from wood, including plywood and OSB, is very common for creating the external envelope of a building. Builders may also use gypsum, cement board or glass-mat sheathing.
Windows: An important component in terms of energy efficiency, double-paned windows are one option that many builders choose to increase insulation and reduce the amount of air escaping from the home. With all windows, proper flashing is critical to create a seal.
Building envelope systems and materials work best, however, when considered as a holistic unit instead of individual parts. And that’s where the LP Structural Solutions portfolio comes in.
Using LP Structural Solutions for a Tighter, More Resilient Building Envelope
Achieving a tight building envelope that also allows room for the structure to breathe is possible with symbiotic products and a holistic system. According to Craig Miles, Director, OSB Sales & Marketing at LP Building Solutions, the answer lies in products designed better overall—and designed to work together.
Miles points to LP WeatherLogic® Air & Water Barrier as an example. “Moisture is the biggest threat to the building envelope,” he says. “LP WeatherLogic panels and our Seam & Flashing Tape inherently keep moisture out.” However, incorporating LP WeatherLogic Water Screen in the exterior envelope adds another layer of assurance that moisture will drain out.
“Water Screen is there to help build a better wall cavity,” Miles says. “You’re never going to have a cladding that is 100% non-permeable, so Water Screen creates a drain and allows gravity to do its work.”
Miles points to the importance of working with a manufacturer invested in innovation for building envelope systems and materials as well. Building better “creates a need for better partnerships,” Miles adds. “Builders will want to have partners who can provide the products alongside the support they need.” When you find a good partner, he continues, you can lean on them, sharing pain points that will inform the company’s innovative steps forward.
“Confidence comes from choosing the right forward-thinking partner,” says Miles.
Check out our portfolio of LP Structural Solutions products for more information on how our building solutions will Defend Your Build® for years to come.
Continue Reading
Resiliency Solutions
5 minIntroducing LP® SmartSide® ExpertFinish® Naturals Collection™: Nature-Inspired Beauty Meets Engineered Performance
We’re excited to introduce the LP® SmartSide® ExpertFinish® Naturals Collection™, a bold new addition to our trusted line of engineered wood siding and trim that delivers the warmth and beauty of nature with the advanced protection and performance builders and homeowners expect.
Labor Solutions
5 minChoosing the Right LP® Structural Solutions Product for Your Build
When it comes to building strong, reliable, and high-performing structures, the materials you choose matter. At LP Building Solutions, we understand that every project, whether it’s a single-family home or a multifamily development, requires structural components that meet your needs for strength, durability, and efficiency.
Sustainability Solutions
5 minBuilding a More Sustainable Future with LP Building Solutions
In today’s world, sustainability is no longer just a buzzword, it’s a blueprint for responsible living and smarter building. As the construction industry seeks ways to reduce its environmental footprint, LP Building Solutions is focused on providing innovative building materials for eco-conscious builders to help reshape what it means to build sustainably
News & Stories3 min
History of Partnership with Gary Sinise Foundation
The LP Foundation is a proud partner of the Gary Sinise Foundation, which supports wounded veterans in several ways. You can learn more about the LP Foundation here.