Business Advice5 min
What Does Energy Star Certified Mean?
Environmentally friendly living continues to be top-of-mind for homeowners. Because many want homes that are built for energy efficiency, professional builders must prepare to discuss this topic with their clients and to provide options for a build that promotes energy efficiency and minimal environmental impact.
The ENERGY STAR certification program is one green building certification homeowners may be familiar with. Let’s take a look at the basics of the ENERGY STAR rating system and learn how you can use products from LP Structural Solutions to contribute to ENERGY STAR certifications.
The ENERGY STAR Label: The Basics
Implemented by the United States Environmental Protection Agency (EPA), the ENERGY STAR program focuses on helping businesses and individuals make more energy-efficient choices, which can help them save money and contribute to a healthier environment.
The program began in 1992 with the goal of reducing greenhouse gas emissions. It expanded in 1995 to include more products, and by 1996 the EPA had connected with the United States Department of Energy to establish additional categories. Today, the ENERGY STAR label is on everything from lighting and home electronics to building materials, and it has contributed to massive energy savings over many years ($24 billion in 2012 alone).
“The overall movement in energy efficiency is to reduce the energy consumption per home,” Neil Freidberg, LP Building Science Manager sums up. “While individually it may not be a lot, whole communities designed to this standard have a large impact on the grid.”
The ENERGY STAR Rating System
For buildings, eligibility for ENERGY STAR certification depends on a score of 75 or higher on the EPA’s 1-100 scale. This indicates that the structure in question performs more efficiently than 75% of similar buildings across the nation. The score is based on measured use of energy in the building and can be calculated via the ENERGY STAR Portfolio Manager tool. Certification is checked for compliance yearly, so structures must maintain their scores to continue achieving certification.
Impacts of the ENERGY STAR Label
The ENERGY STAR rating system doesn’t just provide a label—it creates tangible impacts on the environment. For example, an office building with an ENERGY STAR certification uses 35% less energy, generates 35% fewer greenhouse gas emissions, and may even cost less to operate. When builders focus on structures that also achieve ENERGY STAR certification, they can bring similar savings and reductions to their clients in homes all across the country.
Why Build With ENERGY STAR Criteria in Mind?
When talking with your clients about ENERGY STAR criteria and product selection, being able to communicate the specific benefits of the program is helpful. Here are a few to highlight:
Lower energy bills. “Cost savings is potentially the largest impact,” Freidberg confirms. Your clients will love to hear that choosing energy-efficient products may help them enjoy lower bills in their day-to-day lives. An appropriately sized HVAC unit will run longer and more effectively, which should increase the life of the unit.
Higher resale value. As more homeowners prioritize environmentally friendly assets, homes that already have energy-efficient products may sell for a higher market price. When your clients eventually move, their home’s ENERGY STAR certification may lead to a better resale value and more money in their pockets.
Investment in the future. Green building requirements in many cities are increasing, so getting in on the ground floor now with sustainable choices can help make meeting these requirements easier in the future.
“A benefit that is difficult to put a price tag on is comfort,” Freidberg adds. “Because of all the potential items that an ENERGY STAR home can have, the occupants could see a physical effect where they are comfortable in their home more often.”
LP Structural Solutions and ENERGY STAR Certifications
“Codes have started to include an energy path so that builders can choose how they want to make the homes they build more efficient,” Freidberg says. “They can choose materials, equipment and techniques to achieve a specific level of efficiency.”
When it comes to LP Structural Solutions, LP® TechShield® Radiant Barrier and LP NovaCore™ Thermal Insulated Sheathing both aid in the evaluation of a building to be certified as ENERGY STAR.
LP TechShield sheathing, for example, can help reduce ambient temperature in an attic. “This helps the code-mandated minimum attic insulation to be more effective,” Freidberg explains. “LP TechShield sheathing can reduce the attic temperature by up to 30 degrees Fahrenheit. Without LP TechShield sheathing, there can be an increase in the amount of energy required to cool the ceiling surface. This increases the size and amount of cooling required to make your home comfortable, causing more energy consumption, larger HVAC units and potentially a less comfortable experience for homeowners.”
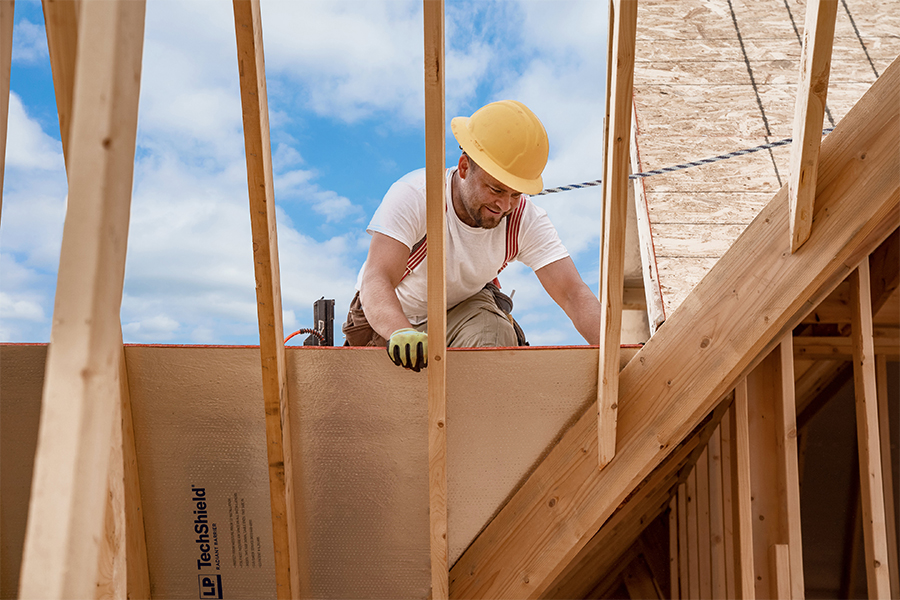
LP NovaCore sheathing can contribute to more efficient wall insulation because it provides continuous insulation, according to Freidberg. “These are things that ENERGY STAR looks for when analyzing products and home performance,” he says.
Interested in Learning More?
“There are several national programs builders can reach out to,” suggests Freidberg. “They can also reach out to home rating companies and ask them for a consultation to look at all the options available based on their climate zones.”
Read more about LP’s dedication to green building here.
Continue Reading
Resiliency Solutions
5 minIntroducing LP® SmartSide® ExpertFinish® Naturals Collection™: Nature-Inspired Beauty Meets Engineered Performance
We’re excited to introduce the LP® SmartSide® ExpertFinish® Naturals Collection™, a bold new addition to our trusted line of engineered wood siding and trim that delivers the warmth and beauty of nature with the advanced protection and performance builders and homeowners expect.
Labor Solutions
5 minChoosing the Right LP® Structural Solutions Product for Your Build
When it comes to building strong, reliable, and high-performing structures, the materials you choose matter. At LP Building Solutions, we understand that every project, whether it’s a single-family home or a multifamily development, requires structural components that meet your needs for strength, durability, and efficiency.
Sustainability Solutions
5 minBuilding a More Sustainable Future with LP Building Solutions
In today’s world, sustainability is no longer just a buzzword, it’s a blueprint for responsible living and smarter building. As the construction industry seeks ways to reduce its environmental footprint, LP Building Solutions is focused on providing innovative building materials for eco-conscious builders to help reshape what it means to build sustainably
News & Stories3 min
History of Partnership with Gary Sinise Foundation
The LP Foundation is a proud partner of the Gary Sinise Foundation, which supports wounded veterans in several ways. You can learn more about the LP Foundation here.