Business Advice6 min
Horizontal Property Regimes: How to Help Prevent Row Home Fires
The trend to live near downtown hasn’t waned in recent years. However, finding empty lots to construct new houses continues to pose a challenge. Builders are finding solutions within the Horizontal Property Regime (HPR) zoning policy, which allows tall and skinny row homes.
However, with as little as six feet between structures the potential for row home fires dramatically increases. Let’s take a look at some of the concerns for both builders and homeowners—and how LP® FlameBlock® Fire-Rated Sheathing can help builders meet code.
What is a Horizontal Property Regime?
By definition, Horizontal Property Regimes allow the construction of two houses on one parcel of land. Traditionally HPRs required units to be connected or stacked on top of one another, similar to typical duplexes and condominiums. Today, HPR zoning has paved the way for tall and skinny row house construction.
Each state has laws defining and governing the specifics of horizontal property regimes. Typically, however, the property owners—or in many cases the builders—must create and record a master deed that outlines details of the regime, including ownership, maintenance and authority. HPRs are very similar, in fact, to condominium HOAs.
What are the Differences in a Horizontal Property Regime vs. a Condo?
HPRs for row houses are very similar to condominium zoning. By definition, condos refer to “common ownership.” While different homeowners own each unit, areas such as pools, halls, stairways, sidewalks and roofs are owned “in common,” and the expenses to maintain or repair them are shared among the owners.
For horizontal property regimes, common ownership extends to fire risk and potential fire damage as fire can quickly spread and engulf a row of tall and skinny houses.
When Do I Need Rowhome Fire Protection?
With as little as six feet between row houses, it can be difficult for firefighters to get between the structures and fight back the flames. As HPR zoning codes are evolving with urban infill, building codes are also adjusting.
Building codes typically require exterior fire-resistance-rated wall assemblies when the fire separation distance becomes small. The fire separation distance is defined in the code as the shortest distance between a building and the lot line or to an imaginary line between two buildings on the same lot.
For example, row homes with only six feet between them have only a three-foot fire separation distance. Since this is less than the minimum five feet of fire separation distance required (without sprinklers), the exterior walls must be 1-hour fire-resistance-rated, with the rating from either side.
The exterior rating provides thermal protection for the neighboring house, and the interior rating works to keep the fire contained in the burning house as long as possible. This requirement changes if there is more than five feet of fire separation between neighboring homes or if the homes are sprinklered. For specific requirements in your area, be sure to check local building codes carefully.
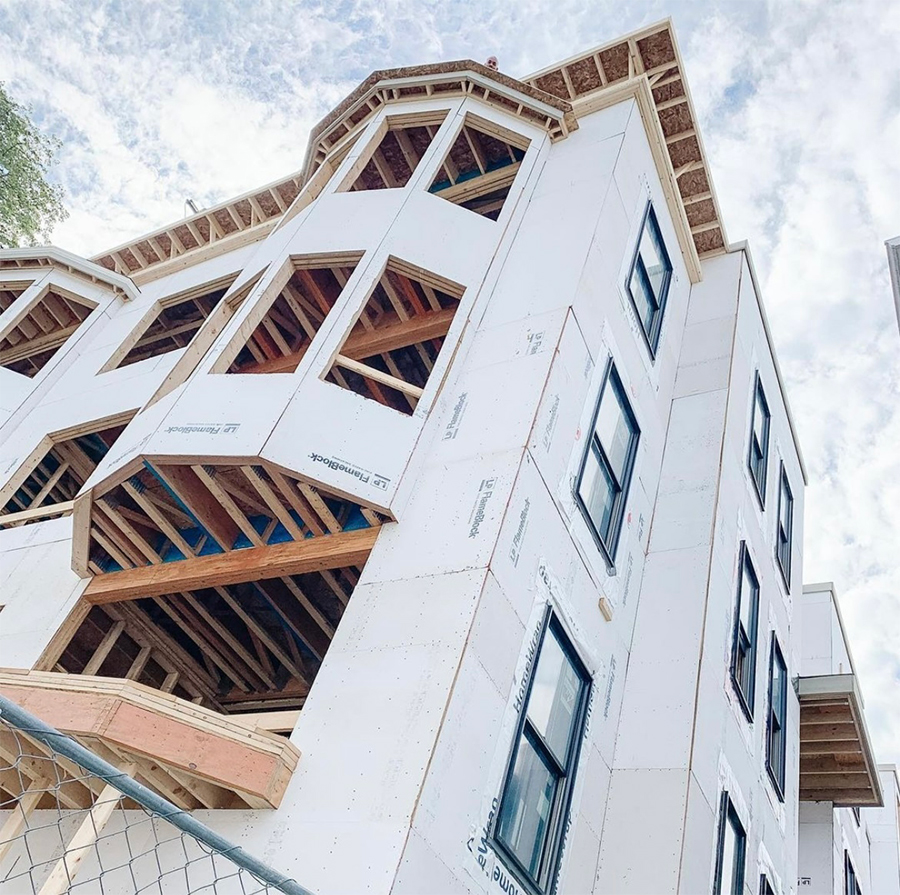
LP® FlameBlock® Fire-Rated Sheathing is especially beneficial in the construction of low- and mid-rise wood structures like tall and skinny row houses. LP® FlameBlock® panels combine flame-spread and burn-through resistance with the structural capacity of OSB sheathing in a single panel, helping reduce damage among HPR-zoned row houses situated on one lot.
To make LP® FlameBlock® fire-resistive panels, LP’s proprietary ignition-resistant, fiberglass-reinforced Pyrotite® coating is applied to the OSB panels. The sheathing allows fire resistance–rated walls to be assembled faster than common alternatives, potentially reducing labor costs while providing exceptional strength, durability and consistency.
Meeting code is just one of the benefits of LP® FlameBlock® Fire-Rated Sheathing. For more information on these innovative assemblies, review our complete guide.
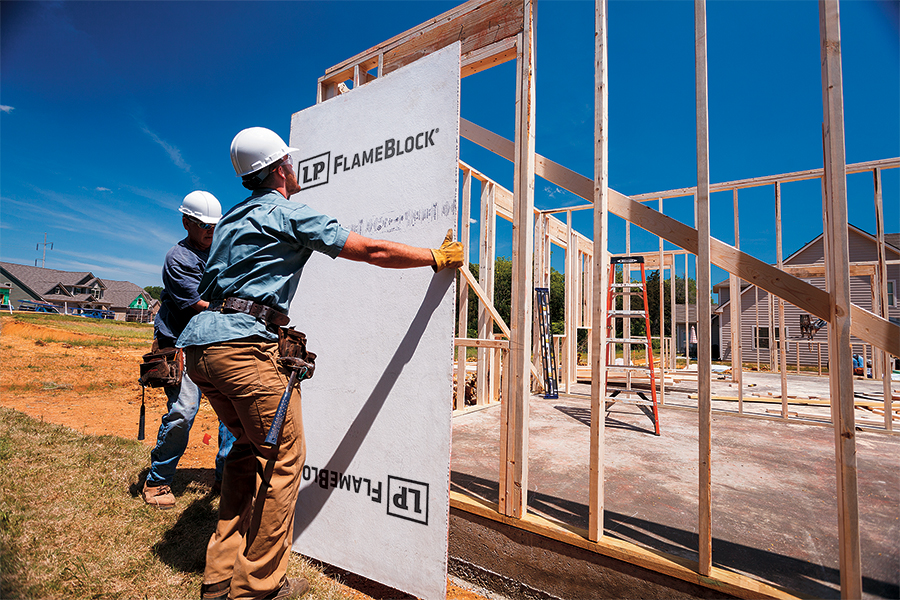
Continue Reading
Resiliency Solutions
5 minIntroducing LP® SmartSide® ExpertFinish® Naturals Collection™: Nature-Inspired Beauty Meets Engineered Performance
We’re excited to introduce the LP® SmartSide® ExpertFinish® Naturals Collection™, a bold new addition to our trusted line of engineered wood siding and trim that delivers the warmth and beauty of nature with the advanced protection and performance builders and homeowners expect.
Labor Solutions
5 minChoosing the Right LP® Structural Solutions Product for Your Build
When it comes to building strong, reliable, and high-performing structures, the materials you choose matter. At LP Building Solutions, we understand that every project, whether it’s a single-family home or a multifamily development, requires structural components that meet your needs for strength, durability, and efficiency.
Sustainability Solutions
5 minBuilding a More Sustainable Future with LP Building Solutions
In today’s world, sustainability is no longer just a buzzword, it’s a blueprint for responsible living and smarter building. As the construction industry seeks ways to reduce its environmental footprint, LP Building Solutions is focused on providing innovative building materials for eco-conscious builders to help reshape what it means to build sustainably
News & Stories3 min
History of Partnership with Gary Sinise Foundation
The LP Foundation is a proud partner of the Gary Sinise Foundation, which supports wounded veterans in several ways. You can learn more about the LP Foundation here.